From Manufacturing Line to Digital Workspace: Navigating Bottlenecks
In a classic manufacturing organisation, spotting a bottleneck is as clear as daylight. Just glance at the production line, and you’ll see materials accumulating in one area – and viola! Right there sits your bottleneck. But these make-or-break points aren’t always so visible in today’s digital workspace. In an environment where digital assets take the place of physical stock, identifying bottlenecks can become a perplexing task.
Tackling Real-world Bottlenecks
I’ve experienced firsthand the shift in identifying these digital bottlenecks. One particular engagement with an organisation building its data and analytics capabilities offered an excellent opportunity to explore this area.
Could adopting tools and techniques help?
The organisation’s data team struggled to deliver high-volume dashboards and data reports – they were stuck in hidden inefficiencies or ‘digital bottlenecks’. Using techniques such as visualising the work through digital Kanban boards on JIRA, applying Work In Progress limit (WIP Limit), we were able to uncover these hidden digital bottlenecks. The figure below shows the Data Team kanban board.
It was evident that tasks began to pile up before hitting the ‘Data Preparation’ stage. This accumulation was a clear sign of demand surpassing delivery capacity, pointing directly to a significant bottleneck. To tackle this, we brought on board an additional data engineer. While this might raise eyebrows among some lean practitioners, the demand for data bricks expertise justified our call. This move boosted productivity, but not for long. Soon enough, work started to mount up before the subsequent stage, unveiling yet another bottleneck.
For those accustomed to process optimisation, such recurrent blockages might feel familiar, like a fatiguing game of ping-pong between different stages within the value stream.
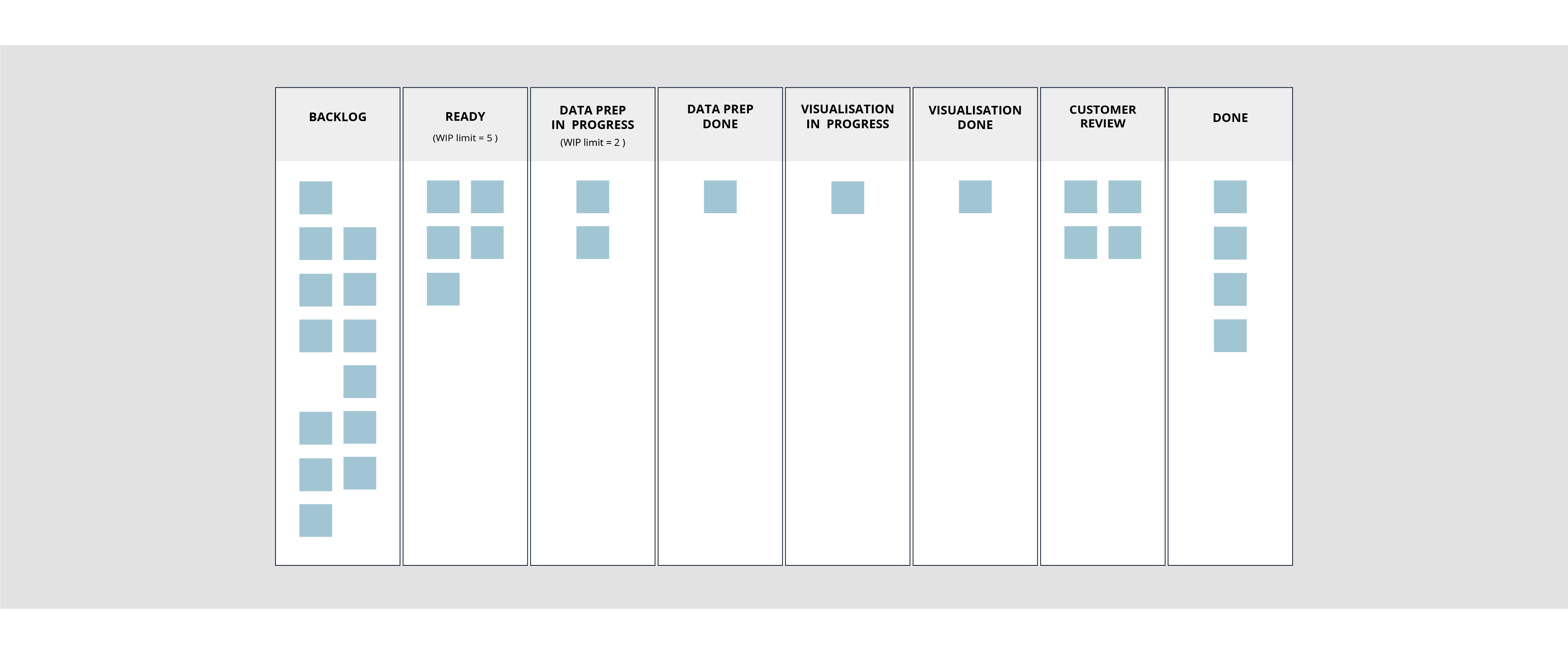
Alternative approach? What if it was T-shaped skills?
Instead of falling into a perpetual “lets hire” the skills as a solution, often chosen by teams plagued by ever-increasing tasks, lack of WIP visibility and workload in general, we inspired the existing team members to enhance their ‘T’-shaped skill set spanning across both Data Engineering and Data Visualisation domains. This encouraged intrinsic motivation in teams to improve. Dan Pink speaks about autonomy, mastery and purpose (Drive: The Surprising Truth about What Motivates Us, Daniel Pink). This allows for flexibility, enabling the team to respond to sudden surges in demand by helping in areas outside their usual remit – all swarming on data preparation if there was a sudden influx of data preparation to do. Increasing flexibility in the team allows them to smooth out peaks in demand and avoid bottlenecks, which improved throughput and allowed the team to produce dashboards faster.
However, our triumph was short-lived as we discovered that we had unknowingly moved the bottleneck downstream, landing right at the customer review phase after delivery, leading to unforeseen challenges.
Streamlining After-Delivery Operations
Examining these downstream bottlenecks unveiled subsequent problems – the downstream teams were raising fix requests and bug identifications weeks after the dashboard was completed, forcing the team to revisit old work, which massively impacted overall productivity. This delay in raising issues was primarily due to unhoned skills within the business to effectively analyse the data being presented in the dashboards and a lack of skill in effectively testing the dashboards after delivery.
Our focus then switched to nurturing downstream teams’ inherent business analysis and testing capabilities while maintaining scheduled bug-fixation hours. As a result, the time taken by the downstream teams to test the dashboards shortened considerably, and the flow/throughput increased. This meant fewer disruptions from revisiting old work and an overall improved efficiency. It’s worth noting that each time we identified and addressed a bottleneck, while it may have illuminated another bottleneck, the overall flow improved from its previous state. This is the essence of continuous improvement: each adjustment leads to better results, even if new challenges emerge.
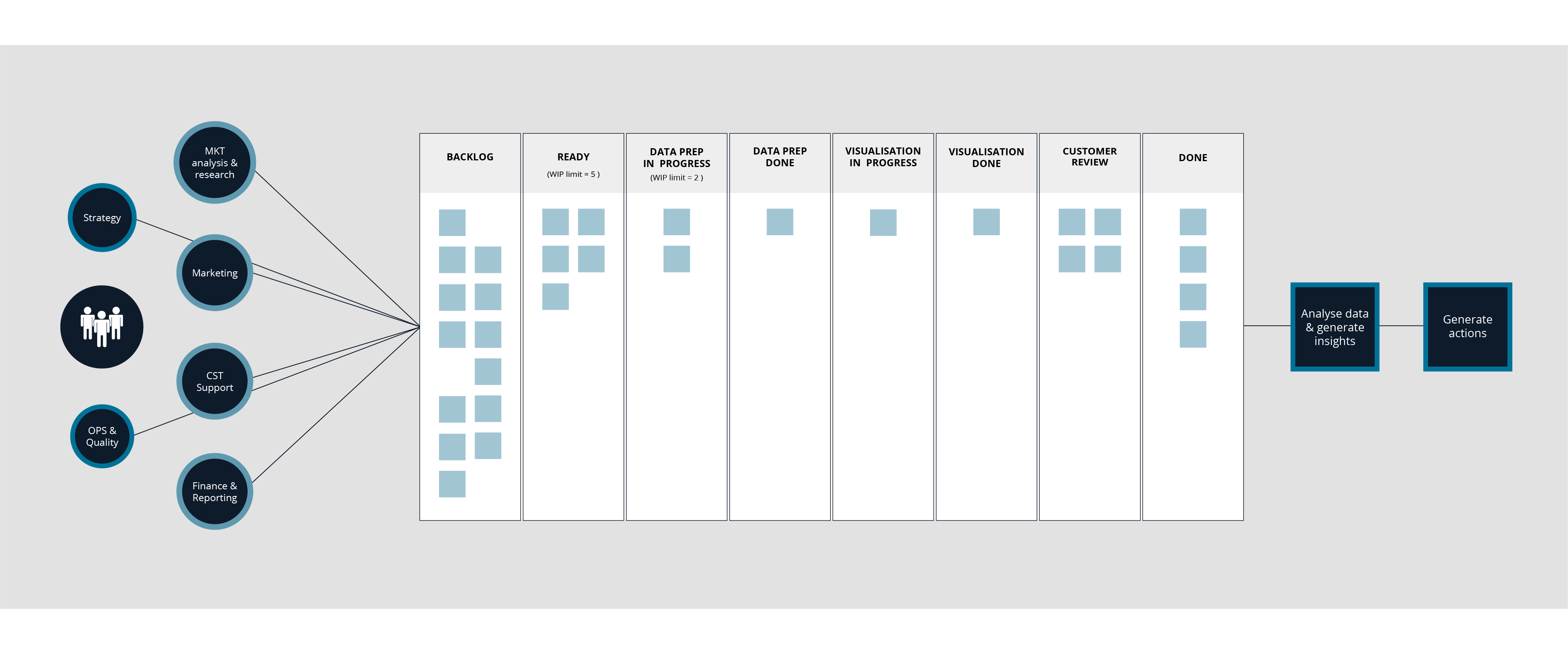
Conclusion: Bottleneck Management Balance
In the dance of bottleneck management, addressing one often shifts the spotlight to another. This isn’t a sign of failure, but rather an inherent trait of systems. Like water flowing in a stream, once you remove one obstruction, the current simply moves to the next. It’s a continuous journey, and that shifting challenge is both normal and expected. It reminds us that there’s always room for growth and evolution in our processes.
However, it’s crucial to understand there’s no instant magic solution. Successful bottleneck management is about fostering a culture of continuous improvement within your organisation. A pivotal tool in this journey is the application of WIP limits. These limits not only make bottlenecks visible, but also act as a valve to manage the flow. By establishing clarity and transparency around issues and methodically addressing them one by one, throughput improves. Without such limits, identifying the exact bottleneck can become significantly challenging.
In some scenarios, strategic placement of bottlenecks can serve as a boon rather than a bane. Imagine owning a popular doughnut shop – having a queue extending out the door often creates an illusion of high demand, which can attract more customers. Thus, these make-or-break points may serve as control valves guiding your productivity flow.
Remember: The goal is not simply about eliminating bottlenecks altogether; instead, it’s all about learning how best to manage them for optimal overall efficiency. And as we’ve seen time and time again, every time we target and address a bottleneck, we enhance the flow from where it previously stood. This journey is the heartbeat of continuous improvement, ensuring that each refinement, regardless of new challenges that arise, still moves us closer to better results.